Cold storage equipment pipeline installation and oil return precautions
19-04-2022
1. The horizontal suction pipeline should have a slope of more than 0.5% along the direction of refrigerant flow; the cross section of the horizontal suction pipeline must ensure that the gas velocity is not less than 3.6m/s;2. In the vertical suction line, the gas flow rate must not be less than 7.6 ~ 12m/s; the gas flow rate greater than 12m/s cannot significantly improve the oil return, which will generate high noise and lead to a higher suction pipe. road pressure drop;3. At the bottom of each vertical suction line, a U-shaped oil return must be set up; if the height of the vertical suction line exceeds 6m, a U-shaped oil return must be set up for every additional 6m; U-shaped oil return The length of the oil should be as short as possible to avoid the accumulation of too much oil;4. The return line should slope towards the compressor at a slope of 3/1000. The exhaust line should slope towards the condenser at a slope of 2/1000. The unit should be as close as possible to the evaporator of the cold storage. When the unit is located higher than the evaporator, an oil return trap should be set at the joint of the horizontal return pipe of the evaporator and the rising riser; if the unit is located much higher than the evaporator, an additional oil trap should be installed every 6 meters of the ascending section.
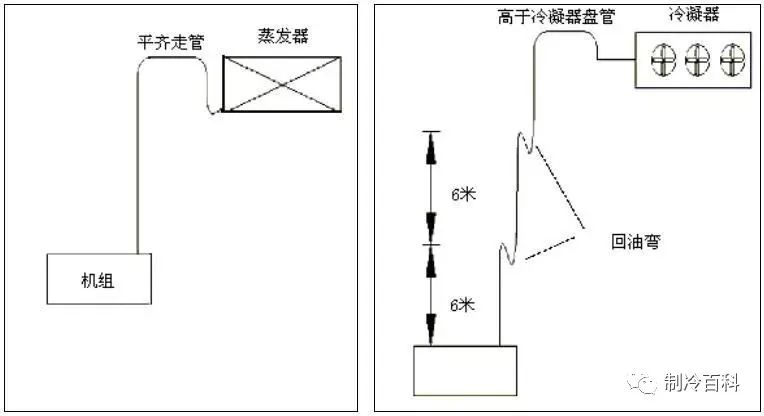
If the unit is lower than the evaporator, the oil trap at the bottom of the ascending section should raise the return gas pipe to be flush with the upper surface of the evaporator, and then run the pipe toward the unit. If the position of the condenser is higher than that of the compressor unit, an oil return bend should be added in the ascending section of the exhaust pipe for every 6 meters of the condenser higher than the compressor unit. In addition, in the system where the one-way cut-off oil return valve is not installed in the exhaust part, the exhaust riser should be raised above the coil level of the air-cooled condenser, and then connected to the condenser.
5. When the system does not use the evacuation cycle, a U-shaped shut-off bend should be set at the outlet of each evaporator to prevent the liquid refrigerant from flowing into the compressor under the action of gravity during shutdown;6. When the suction riser pipe is connected to the evaporator, there should be a section of horizontal pipe and a shut-off bend in the middle for installing the temperature sensing bulb; to prevent the expansion valve from malfunctioning;7. When the compressor is higher than other positions of the system, the oil return bend should be set at about 3m in the rising riser, and the pipe diameter of the return air riser should be reduced to increase the flow rate to bring the oil back to the compressor;
8. Generally, the U-bend installed when the condenser is higher than the compressor is designed to prevent the condensing of the working fluid and the return of the oil when the machine is shut down. In the case of reasonable system pipeline design, when the evaporator is lower than the compressor, it is necessary to consider setting up an oil return bend, and the pipe diameter can be appropriately reduced to meet the oil-carrying speed (especially in low temperature conditions).Generally, the allowable lifting height of the fully hermetic compressor is 4 meters, the allowable lifting height of the semi-hermetic compressor is 6 meters, and the slope of the horizontal pipeline is greater than 1:125; as long as the flow rate of the refrigerant is greater than 4m/s, the lubricating oil can be smoothly taken out ;Double-click the problem of parallel return oil level balance, and installation is also very important. The two compressors must be in the same horizontal position and have the same model (same power), the oil return main pipe must be equally divided between the two units, the branch port must be in a "Y" shape, and the branch pipes must be the same height and length. , the diameter of the pipe is the same to ensure the same amount of oil. Then there is the problem of operation adjustment. For example, the suction pressure of the two machines should be exactly the same, and there must be no flushing phenomenon, otherwise the oil will disappear immediately. If the above cannot be guaranteed, it is impossible for the oil return to be consistent.Maintain higher return air temperature and pressure, increase longer return air pipelines; increase regenerators, etc. Control the opening degree of the throttle valve (expansion valve) well. When the compressor is found to be frosted, the opening degree of the expansion valve should be adjusted in time to control the return steam pressure within a reasonable range.About ten minutes before each shutdown, the liquid supply valve must be closed first, the refrigerant must be stored in the high-pressure components such as the condenser and the liquid accumulator, and the operation will continue, and the liquid level in the evaporator should be lowered before shutdown to ensure the next startup There is no liquid hammer phenomenon. When multiple stages are connected in parallel, pay attention to the balance of gas return and oil return.